به دلیل تنوع وکاربردفراوان فولادها، طرح، وکاربرد هرکدام دریک مقاله امکان پذیرنیست . دراین مقاله ، کوشیده ایم فولادها رابه طورکلی گروه بندی کنیم . فولادها ازنظرعناصرتشکیل دهنده ، به دونوع فولادغیرآلیاژی وآلیاژی تقسیم می شوند .
فودلادهای غیرآلیاژی :
این فولادها از 0.06 تا 1.5 درصدکربن دارند. عناصردیگری نیز با آنها همراه است که درهرحال مقدارآن ها نباید از حد معینی (0.5 درصدسیلیسیم ، 0.8 درصدگوگردومنگنز ، 0.5 درصدآلومینیم یا تیتان ، 0.25 درصدمس ) بیشترباشد. درفولادهای غیرآلیاژی ، کربن نقش تعیین کننده را دارد ،به همین دلیل ،این فولادها به فولادهای کربنی نیزمعروف هستند.
فولادهای آلیاژی :
اگرفولادرابرای افزایش و تامین خواص مورد نظر بافلزاتی مانند کرم ، نیکل ، ولفرام ، کبالت ، مولیبدن ، منگنز ، وانادیم و ... آلیاژ کنند ، فولادهای آلیاژی به دست می آید .چنانچه مجموع درصد وزنی عناصر موجود در فولاد آلیاژی از 5 درصد کمتر باشد، آن را فولاد «کم آلیاژ» و چنانچه از5 درصد بیشتر باشد، «فولاد پرآلیاژ» می نامند. فولادها را از نظر کاربرد به دو نوع فولادهای ساختمانی و فولادهای ابزارسازی تقسیم می کنند.
فولادهای ساختمانی
به فولاد هایی می گویند که از آنها می توان به عنوان مواد اولیه برای ساختمان اسکلت های فلزی ، اسکلت پل ها وهمچنین برای ساختن قطعات وسایل نقلیه ، دستگاهها ، ماشین آلات ، اجزای ماشین (پیچ ومهره ، میله ومحور، یاتاقان غلتشی و ... ) استفاده کرد . امروزه حدود 90 درصد محصولات کاخانه های فولادسازی را فولادهای ساختمانی تشکیل می دهند . تقسیم بندی فولادهای ساختمانی در نمودار شکل زیر نشان داده شده است
فولادهای ساختمانی معمولی :
این فولادها جزء فولادهای غیرآلیاژی هستند و چون درانتخاب آن ها استحکام کششی نقشی تعیین کننده دارد ، آن ها را برحسب استحکام کششی شان طبقه بندی می کنند . استحکام کششی این فولادها متناسب با درصدکربن موجود در آنها افزایش می یابد و برعکس ، انبساط (کش آمدن ) آنها کاهش می یابد ،. به عبارت دیگر، با افزایش کربن ، شکنندگی فولادبیشترمی شود . همچنین ازدیاد کربن قابلیت تغییر فرم درحالت یا گرم ، قابلیت جوشکاری ، و براده برداری فولاد را کاهش می دهد . این فولادها از 0.12 تا 0.6 درصد کربن داشته وآنها رادرسه گروه با درجه مرغوبیت 1و 2 و 3 تولید و به بازار عرضه می کنند .
فولادهای دانه ریزمخصوص جوشکاری :
این فولادها قابلیت جوشکاری خوبی دارند .
فولادهای سختکاری شونده (کربوریزه ) :
ازاین فولادها برای ساختن قطعاتی استفاده میشود که بایستی دارای سطح خارجی سخت وقسمت داخلی (مغز ) نرم باشند. همچنین سطح آنها درمقابل سایش مقاوم بوده وقسمت داخلی آنها قابلیت تحمل خودرادرمقابل ضربه حفظ کند وشکننده نباشد . برای این منظور، ابتدا کربن سطح خارجی آن ها رابا روش های مختلف افزایش می دهند وسپس سختکاری می کنند . برای اینکه قسمت داخلی این فولادها پس ازسختکاری ، نرم باقی بماند ، باید مقداردرصد کربن آن ها از2.0 درصد کمترباشد
فولادهای بهسازی شونده :
این فولادها جزء فولادهای ساختمانی هستند و2.0 تا 6.0 درصد کربن دارند . استحکام کششی ومقاومت این فولادها رامی توان به وسیله بهسازی ( سخت کردن وبرگشت دادن تا درجه حرارت 500 تا 700 سا نتیگراد ) افزایش داد فولادهای بهسازی شونده برای ساخت قطعاتی به کار می رود که درمعرض ضربه وبرخورد قراردارند ،. مانند میل لنگ ها ، محورلنگ پرس های ضربه ای ومحور وسایل نقلیه .
فولادها ی اتوما ت :
این فولادها که به آ نها « فولادهای خوش تراش » نیز می گویند ، جزء فولادهای ساختمانی هستند . استحکام این فولادها برحسب درصد عناصر موجود در آن ها متفاوت است . در هنگام براده براری از این فولا دها ، براده های کوتاهی جدا می شوند وسطح خوبی را به دست می دهند . این ویژگی بیشتراز همه مرهون وجود گوگرد (s ( است که مقدار آن دراین گونه فولادها به 18.0 تا 0.4 درصد می رسد . وجود گوگرد باعث می شود که فولاد گرم شده ، شکننده شود هنگام براده برداری براده های کوتاهی به وجود آید . به همین دلیل درماشینهای اتومات که براد ه های بلند اختلا لات فراوانی ( مانند پیچیدن براده به دور ابزار وکار ، سا ییدگی وکم شدن دوام ابزار ) رابه وجود می آ ورند ، از فولادهای اتومات استفاده شود . شایان توجه است که وجود گوگرد زیاد دراین فولادها ، استحکام آ نها رادر مقابل ضربه کاهش می دهد . از دیگر معایب فولادهای اتومات عدم قابلیت جوشکاری وتغییر فرم سرد آ ن ها است . فولادهای اتوما ت ( بجزگوگرد ) دارای 07.0 تا 65.0 درصد ، 6.0 تا 5.1 درصد منگز 05.0 تا 40. درصد سیلیسیم هستند ودرصورتی که شکنندگی بیشتر براده وسطح مرغوبتر موردنظر باشد ، 15.0 تا 3.0 درصد سرب نیز به آن می افزایند.
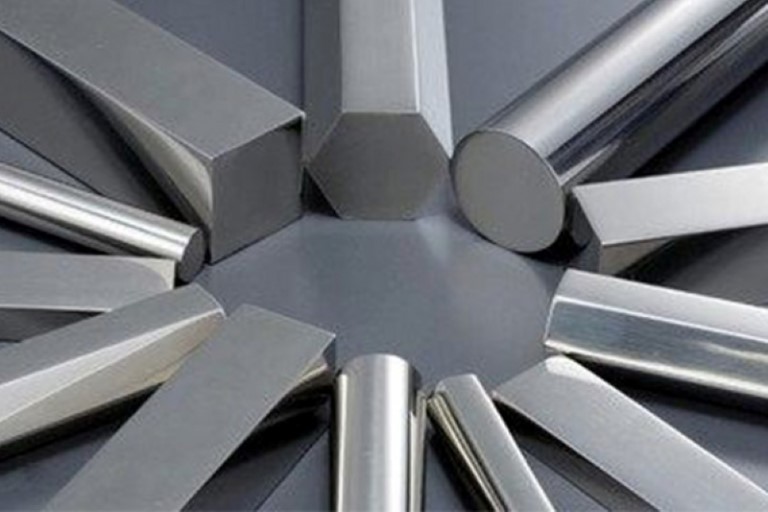
فولادهای فنر :
فولادهای فنر علاوه بر استحکام کششی زیاد ، باید خاصیت الا ستیسیته خوبی داشته ودربرابر سایش وارتعاش نیز مقاوم باشند . وجود سیلیسیم درفولاد فنر خاصیت الا ستیسیته ووجود کرم استحکام ومقاومت درمقابل خوردگی را افزایش می دهد . این ویژگی ها تنها به درصد عناصر موجود در فولاد بستگی ندارد بلکه با وجود آن ها می توان به وسیله ی عملیات حرارتی وتغییر فرم درحالت سرد، خواص آن را تغییر داده و ویژگی های مورد نظر را به دست آورد . فولادهای کربنی با 5.0 تا 1 درصد کربن ، 3.0 تا 4.0 درصد منگز و حداکثر 04.0 درصد گوگرد وفسفر درساخت فنرها کابرد زیادی دارند . برای سا خت فنرهای تخت یا مارپیچی که پس از سا خت تحت عملیات حرارتی قرار نمی گیرد ، فولادهای سخت کشیده یا نورد شده به کار می رود . از فولادهای کرم ووانادیم دار ، درساخت فنرهای بزرگ اتومبیل ولکوموتیو استفاده می شود . فولادهای سیسیلیم دار نیز در سا خت فنرهایی کاربرد دارند که استحکام ومقاومت ضربه ای زیاد از آن ها انتظار می رود . این فولادها به طور متوسط 4.0 درصد کربن ، 75.0 درصد سیسیایم ، 95.0 درصد منگنز با مس یا بدون مس دارند ولی مقدار سیسیلیم آن ها ممکن است تا 2 درصد نیز برسد . فولادهای منگنز دار مخصوص ساخت فنر خودروها محتوی 25.1 درصد منگنز ، 4.0 درصد کربن ، 2درصد منگنز ، و45.0 درصد کربن هستند . استحکام کششی این فولادها به شرط انجام عملیات حرارتی تا 1400 نیوتن برمیلیمتر مربع افزایش می یابد . فولادهای سیسیلیم منگنز دار دارای استحکام کششی زیاد تا حدود 1850 نیوتن بر میلیمتر مربع هستند . نوعی از این فولاد که 64.15 درصد کرم ، 38.4 درصد نیکل ، 68.2 درصد مولیبدن ، 1درصد منگنز ، 32.0 درصد سیسیلیم ، 12.0 درصد مس و14.0 درصد کربن دارد ، درساخت فنر موترهای جت وسایر مواردی که مقاومت در مقابل گرمای زیاد مورد نیاز است ، به کار می روند . نوع دیگری از فولاد فنر با 50 درصد کبالت ، 20 درصد کربن کرم ، 15 درصد ولفرام و10 درصد نیکل وحداکثر 15.0 درصد کربن ، ودر دمای 760 سانتیگراد ویژگی های خود را حفظ می کند .
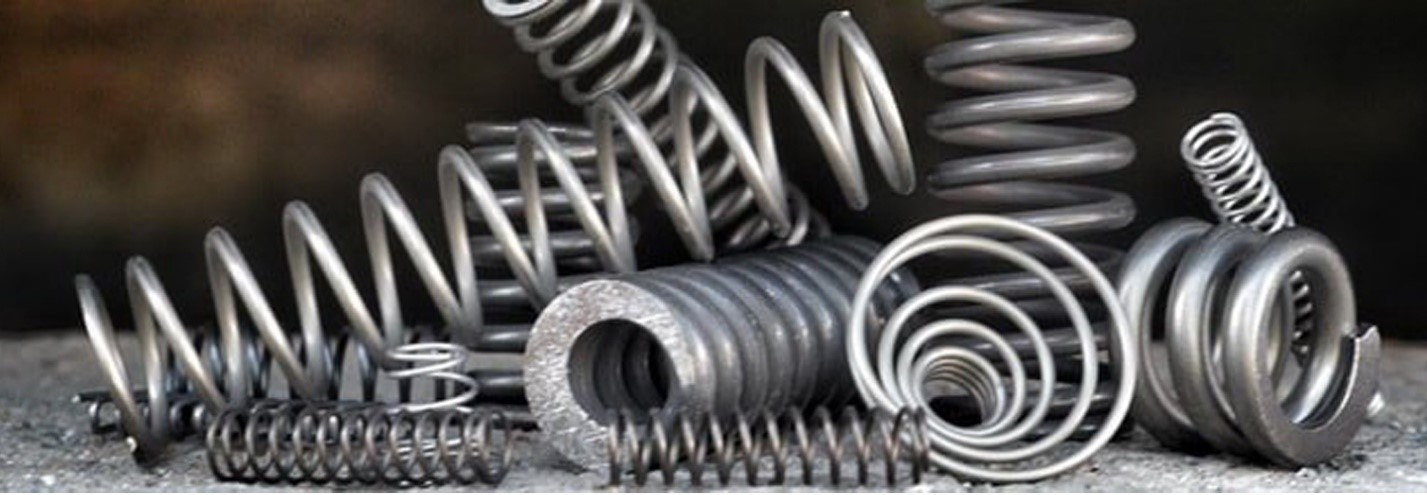
محمدرضا
1403/07/24لطفا منبع خبر را ذکر کنید